Runway Roller for Grass Airstrips
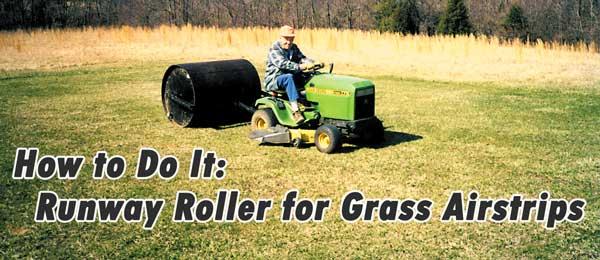
How to Do It: Runway Roller for Grass Airstrips
By Lonnie D. Goad | Photos courtesy the author
As seen in the July 2003 issue of Model Aviation.
I am a member of a small (27 members) AMA chartered club: the Electronic Flyers of Virginia. We operate and maintain a Radio Control flying site on undeveloped Sherando Park property of the Frederick County Parks and Recreation Department in Frederick County, Virginia. The site consists of a grass runway, a pit area, a small shelter, and a parking area.
The winter weather here is such that the runway freezes and is subject to becoming uneven. The club has used various means to have it rolled in the spring to make it more smooth and suitable for its purpose. For a few years we paid a local contractor to roll it with a powered roller, but the cost became more than we wanted to pay. We have also rented a pull-behind roller on occasion.
Rough fields can take a severe toll in landing gear damage. This easy-to-construct roller can smooth out your club’s field.
Some of the other clubs in our area have rollers filled with, or made from, concrete, and they leave them on-site. Since our location is remote and subject to periodic vandalism, there would be a risk if we decided to do this. In addition, we have added a second site at a closed landfill in Warren County, Virginia, and because of the weight involved it would be hard to move such a roller from site to site.
With those conditions in mind, it seemed that a large roller that could be filled (or partially filled) with water when it would be used and emptied when it wouldn’t be in use or when it would be moved around would be ideal for our needs. The initial investment would be significant, but the cost would not be excessive spread out over a period of years.
I set about to have a roller made that the club could use as needed. With club members volunteering to do the hauling from site to site and the rolling using their lawn tractors to do the pulling, they could keep the runways in good condition with little, if any, additional expense to the club.
The roller is made from a section of 36-inch-diameter steel pipe, which is 3 feet, 10 inches long, with 1⁄4-inch-thick steel-plate ends. Pieces of 3-inch steel channel iron were used for the frame and tongue, and 11⁄4-inch-diameter steel was used for the shaft. Flanged pillow blocks were used for bearings, and other miscellaneous steel and hardware was used as required.
Pipe collars were used for the filling and vent openings, with plastic plugs. An additional fill plug was drilled with a vent hole (plugged with wire mesh) and is installed when the roller is not in use to prevent pressure buildup and the entrance of insects and the like. (See the materials list and sketch for additional details.)
On our first attempt, we filled the roller approximately half full of water and rolled the runway at one of our sites. The ground was rather dry and hard, but we saw some improvement in spite of the less-than-ideal rolling conditions.
In the spring of 2001 we used the roller at both of our flying sites. At the first field it was filled roughly half full of water, and at the second site it was filled approximately three-quarters full. The roller’s estimated weight when empty is 700 pounds. The water to fill it half full adds roughly 725 pounds, and to fill it completely adds approximately 1,450 pounds.
When used as indicated in the preceding, the lawn tractors pulled the roller nicely. Even though it weighed nearly 2,150 pounds when full, the tractors did not have any trouble pulling it because of the large diameter of the roller and the lubricated bearings.
If your club is in a similar situation, perhaps you could make good use of a roller such as this one. If so, feel free to use any of the information included in this article.
Runway Roller Materials List
- 36-inch-outside-diameter (OD) steel pipe, 7⁄16 inch in thickness
- 1⁄4-inch-thick sheet of steel (for ends)
- 1-1⁄4-inch steel shaft
- Flanged pillow blocks (for bearings): four-bolt square flange, 1-1⁄4-inch shaft size, 3-5⁄8-inch hole centers, 1⁄2-inch bolt size—McMaster-Carr, number 5967K56 (single-row, self-aligning, deep-groove ball bearings, double sealed)
- 3-inch channel iron (for frame)
- 1⁄2-inch-thick x 2-inch-wide steel bar (for hitch)
- 1⁄2 x 1⁄2-inch steel bar (for bracing)
- 1-1⁄2-inch steel collar
- 1-1⁄2-inch plastic plug
- 2-inch steel collar
- Two 2-inch plastic plugs



Add new comment